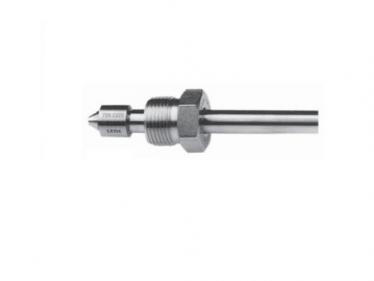
Return to previous page
High pressure connectors
SITEC High pressure connectors are designed for a safe and reliable connection of high pressure tubing up to 10.000 bar.
Specifications | |
Pressure | max 10.000 bar / 145.000 PSI |
Features and advantages
- The male cone on the tubing has a slightly smaller included angle of 58° than the 60° female cone. The initial line contact between the two cones has a theoretical area equal to zero. Low-torque gland nut loads create stresses that produce localized yielding and plastic flow at the seal contact. As the gland nut is torqued to specified values, the line contact broadens to an annular area seal just wide enough to support the sealing thrust.
- This mechanism obliterates surface irregularities remaining after machining. Leakage paths, for even the smallest molecules, are eliminated. The ultimate in sealing efficiency is achieved with comparatively low torques. Properly tightened the connection can be broken and remade innumerable times.
- Should unusual circumstances produce a leak at the seal, full system pressure could be imposed across the large area defined by the gland nut diameter. Failure of the gland nut thread might result. The weep holes prevent this and faciliate leak detection.
- The cone-to-cone seal provides other unique advantages in comparison with metal-to-metal line seal connection designs which employ tube gripping and sealing members between the tube and the seat. There is only one seal. End-load area is much smaller. The reduced wall section at the seal permits a pressure-energized sealing effect as the tube tries to expand. Differential thermal expansion effects are minimized. Collar and tube engagement is positive with no need to generate a frictional, cutting or swaging action for end-load support.
- This standard for high-pressure technology has won rapidly growing acceptance throughout the world because of its reliability and ease of installation.